We are excited to announce our newest high-performance autopilot, specially designed for advanced/professional users who require the best of the best with minimal space.
The mRo Control Zero is the first autopilot jointly designed by Nick Arsov, Phillip Kocmoud, and Jordi Muñoz. Together, we have developed many of the autopilots you already know and rely on, including the ArduPilot1, APM, APM2, APM2.5, PixRacer, X2.1, along with many other custom designs powering customer solutions. Our experience, combined with extensive industry and user feedback, are all factored into the creation of mRo Control Zero.
Sensors!
The Control Zero is a clean sheet design with triple IMU sensors. It features the ICM-20948 9DOF (3-axis accelerometer, gyroscope, and magnetometer) which is based on the legendary, field-proven, and fully supported MPU-9250 and the ICM20602 6DOF (3-axis accelerometer, gyroscope), both with several thousand hours of flying.
Also, we squeezed in the new German-made Bosch BMI088 6DOF that features a proprietary internal vibration dampening system specially designed for aerial robotics. Together with the ICMs, this combination will ensure the best performance in all situations.
The newly included DPS310 barometer is more sensitive than the venerable MS5611 without the noise and light sensitivity.
Built for Builders!
Control Zero, at its core, is a universal development board! The mRo Control Zero comes fully supported by PX4 [Coming soon] and Ardupilot. If you require further customization, the Control Zero will come with all the libraries and examples that will allow you to initialize and access all the board sensors and functions directly via our reference code.
Yes, you will be able to create your custom software for this board in no time; no need to worry about initializing everything (we did it for you). The software is written in C and utilizes a free, easy to install, Eclipse-based IDE that is supplied by ST. All is included for free with the sole purpose of giving you access to learn, edit, and improve. Be sure to read and understand ST Hardware Abstraction Layer (HAL) license.
But… be aware of the “limitations” of C; any careless handling of a single byte can potentially provoke a buffer overflow (don’t worry, it won’t damage the board). But hey, this how we all learned at some point, right? The recommended IDE also supports C++ so that you can jump to objects anytime you wish.
You Are Covered!
The mRo Control Zero comes heavily shielded from EMI and highly static hands, so feel free to use your grandma’s polyester sweater while handling the board. Many cloned autopilots come with some potential design flaws that, if manipulated improperly, will permanently damage the board. We know you might have burned one (or two)!
The Control Zero has multiple independent power supplies, internal voltage sensing, EMI shielding, resettable fuses, and buffered PWMs.
The PWM outputs are level-shifted to 5V for optimal noise reduction and compatibility across all consumer and commercial ESC devices, with a total of 8 output channels, each with DMA support for 8x dShot devices (yep, they are all bi-directional). Every pin exposed is protected.
The PCB is a 6-layer stack with an optimized concentration of copper that ensures excellent heat dissipation, but the F7 and H7 microcontrollers are more power efficient and therefore dissipate less heat compared to the all F4 microcontrollers.
Lastly, the mRo Control Zero has a conformal coat to protect it from the environment. Conformal coating is an acrylic layer that covers most of the electronic “pads” — leaving exposed only the sensors that require direct atmospheric contact, like the pressure sensor and the buzzer.
Small is More!
mRo Control Zero comes with several Input/Outputs to cover demanding applications. From 6x serial ports (from which one can be optionally used as SPI), three have flow control, one with I²C and two with just TX/RX will likely satisfy most full-asynchronous communication needs.
Enough outputs to control stuff, all of the 8x PWMs are EMI protected, level-shifted to 5V, fully bi-directional, and attached to DMAs for DSHOT compatibility (yep, all eight of them).
Controller Area Network (CAN): as mRo and the industry moves more and more sensors to CAN, the Control Zero comes fully prepared for this flexible/robust protocol with its built-in CAN transceiver. Just plug and play to any compatible CAN device.
Plenty of R/C Receiver options! The -seventh- advanced-flex serial port onboard the Control Zero allows us to support multiple R/C Receiver Protocols using the same pins, saving us some space. You will have no problem using protocols like FrSky (In & Out), S.Bus, Spektrum w/ Binding, and PPM. Also, comes with a dedicated RSSI input.
Connectors and More.
Designing a miniature system comes with many challenges and limitations. We had a long internal debate about what kind of interface we should use (the way you connect stuff to the board). We had three possible options: pin headers, a single connector, or just exposed pads that required soldering (commonly found in Drone Racers).
Option 1:
Option 1 was a clean and straightforward approach. But, because of the non-standard pin separation that would require an interface board, from this option, the mRo Control Zero OEM was born, specially designed for system integrators.
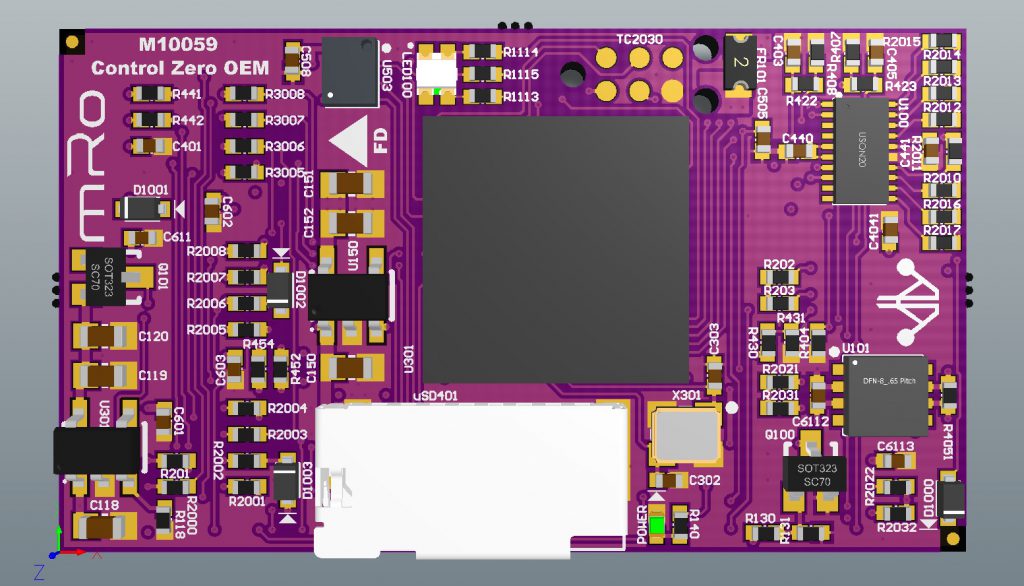
Option 2:
The second option was just to leave the pads exposed as many racer controllers do, but the board was so small that it would’ve been a big challenge for the average user to solder those. Plus, it had the limitation that you wouldn’t be able to remove it from your vehicle that easily, unless you de-soldered everything (kind of a nightmare), so we declined this one. Still, you can order the OEM version without headers pre-soldered and walk down this road, it is up to you.
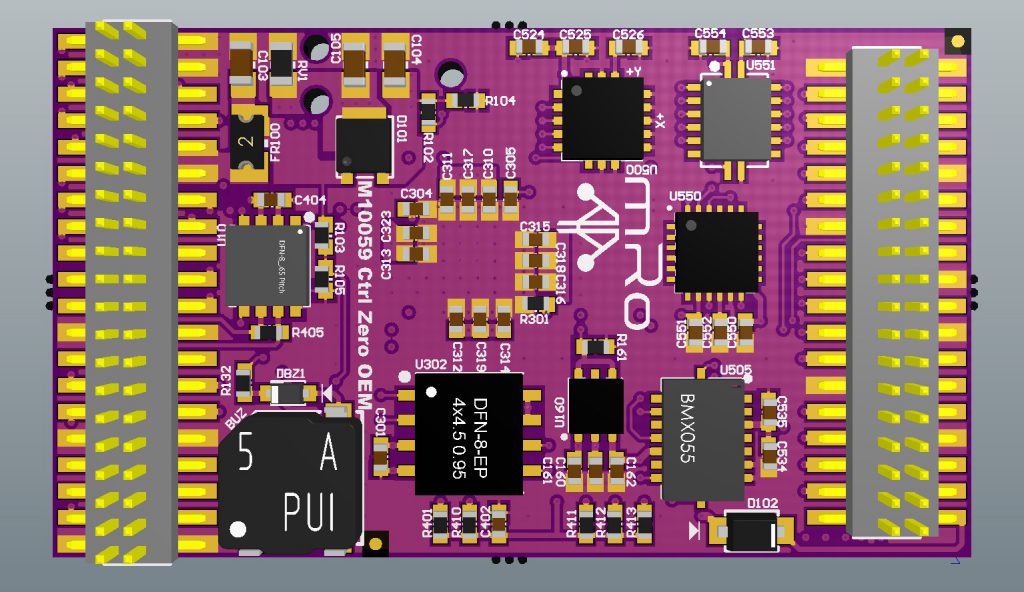
Option 3:
The last and third option was the use of a single connector. This allows the construction of custom harnesses and the ability to easily snap it in & out of the vehicle. Unfortunately, using a single connector was not possible because it would have increased the size of the board too much, among other “stiffness” issues, so we opted for the “two connectors.” This gave birth to the Control Zero and the connector of choice: the Pico-Clasp series by Molex (among other applications, they claim they are designed for aerial vehicles).
Another advantage of using the two-connector approach is the ease with which you can customize your cables. We will provide you with plenty of pre-crimped wires configured in different flavors and enough spare sockets. In conclusion, you only have to insert the wires really needed for your particular setup.
If you require more, insert more, or if you change your mind, just pop the cable out. Broke it? Replace it with a new wire.
Yes, it might be an uncommon approach, but it is actually very easy. Inserting the crimps into the socket only takes seconds or minutes (if you are new) and is way easier and faster than soldering, plus this will result in a minimal weight and overall cleanliness of your setup.
After 11 years of experience building drones, we have seen a thing or two and we know you will love it.
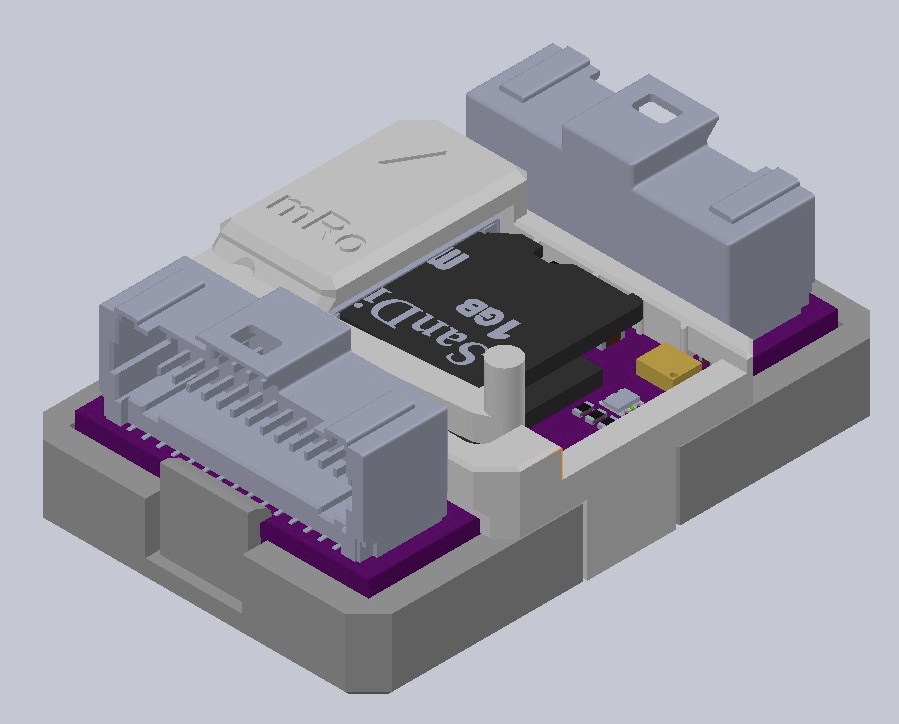
One Architecture, Numerous Possibilities.
We carefully planned the mRo Control Architecture since day ZERO; the software is flexible enough to support any vehicle and so is our hardware.
In other words, if Control Zero is not the right fit for your mission later on, then you can try another variant, like the Ctrl-zero OEM (photos above).
Ctrl-zero OEM is the variant for system integrators. We are also planning to offer the Control Zero Classic with classic DF13 connectors, Control Zero CAN minimal board for dedicated CAN solutions, Control Zero EZ with built-in OSD & Power module, and Control Zero Pro/Max; the biggest variant with all possible I/Os using convenient JST-GHs connectors.
Different boards, different sizes, but all are sharing the same standardized pin assignations and sensor orientation (even bootloader)! This approach allows you to jump up and down from our boards with minimal to no changes to your platform configurations.
More Information
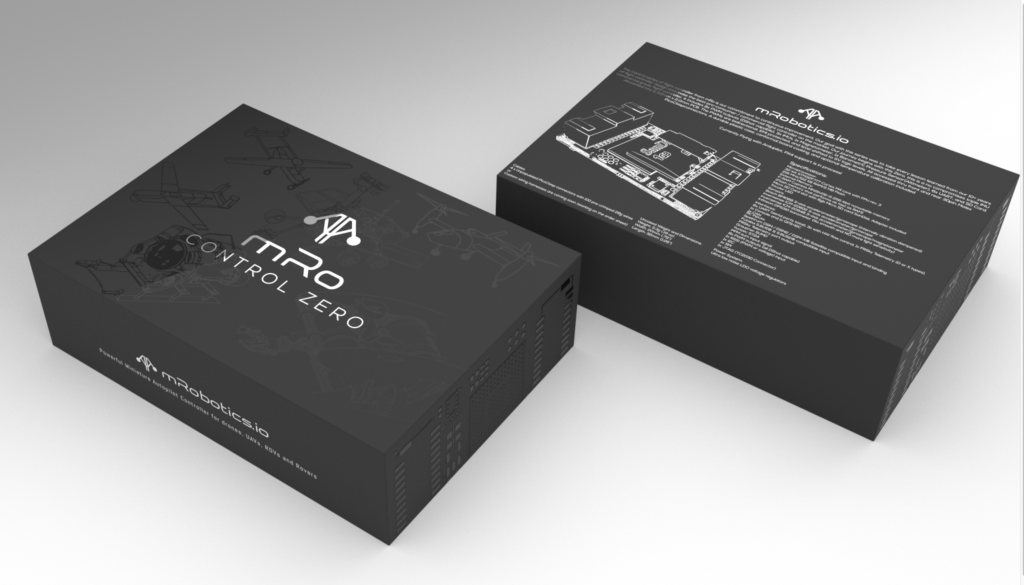
The mRo Control Zero is available for pre-order here; this is an early release and only recommended for advanced users. We assure you we are working as fast as we can.
We estimate that our first orders will go out in early June 2019.
Prototypes are flying! At least we know it can fulfill its purpose.